FP 100 Regulator for BIB AUTOLINE automatic bag in box filling and packaging line
Part of automatic line for filling and packaging liquids in Bag in Box packs
FP 100 Regulator Characteristics
IC Filling Systems offer buffer tank regulation solutions designed to optimise level and flow management during filling operations.
FP 100 regulators are installed between your filtration system (or pasteuriser) and the filling machine. Our equipment optimises metering precision, does not consume nitrogen during production and guarantees high-quality filling without added oxygen.
FP100 Advantages
- Precision: real-time management probe, perfectly controlled levels and flows
- Safety: presence of a safety valve set at 2 bars and a safety probe inside the tank
- Materials meet the 97/23/CE Machine Directive requirements
- UL and CSA Conform configurations available
FP 100 is the solution for optimising level management for Bag in Box Filling under nitrogen pressure during filling operations
FP100 Capacity
100 Litres
FP100 Characteristics
- Air supply: 6 to 6.5 bars
- Nitrogen supply: 2.5 bars
- Power supply: 3 x 400 V + N + T – 50 Hz
- Connection: liquid intake ∅ 40 DIN
- Liquid feed: Max 2 bars (see section 3.D)
- Footprint
- Depth: 800 mm
- Height: 2000 mm
- Width: 600 mm
- Weight: 110 kg (empty)
FP100 Standard Equipment
Automated buffer vat controlled by analogue probe
Complete equipment includes:
- Cylindrical 304 stainless steel vat, 100 litres (useful capacity approx. 50 litres), sterilizable, equipped with two diameter 40 stainless steel butterfly valves + full drainage on rounded bottom, with cover + handle + perforation for injection of inert gas, 304 stainless steel chassis mounted on castors with kit for attaching to the filling machine
- Stainless steel level probe = two measuring points with positioning and connection to the pneumatic valve
- Pneumatic vat inflow valve interlocked to high and low vat levels
- Electro-pneumatic control box with the following functions:
- Stop – go (for pump or heat source)
- Production or cleaning
"I have absolutely no qualms in recommending IC Filling Systems as a good and reputable company to deal with."
- Jim Quigley, Bottling Manager, Inver House Distillers.
“IC Filling Systems provided our first bottle line that never let us down despite the incredible work load it was asked to perform. As more equipment arrives to further reinforce and advance not just the Mk2 bottle line but the business as a whole, IC Filling Systems will remain our partner of choice. Reliable, consistent and robust.”
- Iain Kerr, Wolfburn Distillery
"IC Filling Systems installed a new 7,000bph 20-20-5 Neck Handling PET Filler which we are extremely satisfied with. We were provided with excellent customer support from start to finish as well as being provided with a dedicated project engineer to assist with the whole process. Thanks to all the team at IC Filling Systems."
"Purchased a beer filter, 2 head keg filler and 551 bottle filler. We have received great support and our machines are running very well."
- Eben Uys, The Mad Brew Master, Mad Giant, South Africa
"We have worked with a whole host of people since we started in 2017, and by far, the best people we have worked with during that time was Forysths, and I never thought we would work with someone that matched them, but IC Filling Systems did, and in particular, Alessandro was a joy to work with, he was brilliant!! So good to learn from and a great teacher. He is an asset to the company! We would definitely recommend IC Filling Systems to whoever might ask."
- Michael Morrison, Managing Director, Isle of Barra Distillers
Checking...
Retry »
Sending message...
Send us your enquiry today...
Tell us what you need, and we'll respond promptly.
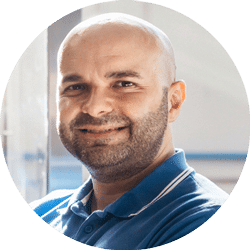
For detailed information
Contact our Sales Director Marco Solferini by calling
+39 0141 162 0091 or +39 0141 74166 (Italy)
+44 1865 520 083 (UK)
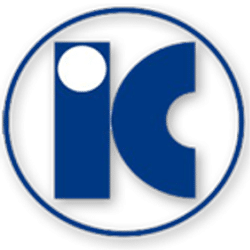
Alternatively request
a quotation
Can’t find what you’re looking for?
Search this site...