Bottle Sleeving Machines
Automatic bottle sleeving machines are used both for full body decoration or only as Tamper-evident Seal.
IC Filling Systems offer both Linear and Rotary machines, for different applications and production speeds.
Our sleevers can apply Decorative Full body sleeves, Tamper evident safety seal sleeves and promotional sleeves.
A steam heat shrink tunnel typically is equipped with:
- 2 devices for steam injection with modulating valves
- 4 steam injection cells with expansion jets
- Adjustable cells support
- Exhaust pipe for condensate
- Exhaust fan for excess steam, electronically managed
- Electronic regulation and constant control of the temperature in the tunnel
- Device for steam heating (electric resistance)
- Visualization on display of the temperature set up in the tunnel
- Visualization of the real temperature of the tunnel
- Control feeler for management of tunnel temperature
- Manometers for pressure regulation in the stages
- Interception valve for manual closing of the steam line (Spirax Sarco)
- Steam separator and steam trap (Spirax Sarco)
- Pressure reduction with manometer (Spirax Sarco)
- Glass doors
- Frame completely clad in stainless steel
- Electrical switchboard in stainless steel
A full body Automatic Bottle Sleeving Machine applicator is normally equipped with the following:
- Frame completely clad in stainless steel
- Screw-conveyor, mandrel and program
- Motorized haulage rollers for "high frequency" insertion, with automatic opening and regulation
- Rollers for reel pulling with automatic opening and regulation
- Automatic control of cut in register and feed of the sleeve
- Head with rotating blades
- Electronic cards for high speed sleeve insertion
- Synchronized motors for high speed insertion
- Brushless motor for reel unwinding with variable speed
- Photoelectric cell in entrance to increase the speed
- Anti-stoppage photoelectric cell in outlet
- Stainless steel switchboard with PLC OMRON
- Accident prevention protections in accordance with CE regulations
- Photoelectric cell to adjust the film length
"I have absolutely no qualms in recommending IC Filling Systems as a good and reputable company to deal with."
- Jim Quigley, Bottling Manager, Inver House Distillers.
“IC Filling Systems provided our first bottle line that never let us down despite the incredible work load it was asked to perform. As more equipment arrives to further reinforce and advance not just the Mk2 bottle line but the business as a whole, IC Filling Systems will remain our partner of choice. Reliable, consistent and robust.”
- Iain Kerr, Wolfburn Distillery
"IC Filling Systems installed a new 7,000bph 20-20-5 Neck Handling PET Filler which we are extremely satisfied with. We were provided with excellent customer support from start to finish as well as being provided with a dedicated project engineer to assist with the whole process. Thanks to all the team at IC Filling Systems."
"Purchased a beer filter, 2 head keg filler and 551 bottle filler. We have received great support and our machines are running very well."
- Eben Uys, The Mad Brew Master, Mad Giant, South Africa
"We have worked with a whole host of people since we started in 2017, and by far, the best people we have worked with during that time was Forysths, and I never thought we would work with someone that matched them, but IC Filling Systems did, and in particular, Alessandro was a joy to work with, he was brilliant!! So good to learn from and a great teacher. He is an asset to the company! We would definitely recommend IC Filling Systems to whoever might ask."
- Michael Morrison, Managing Director, Isle of Barra Distillers
Checking...
Ouch! There was a server error.
Retry »
Retry »
Sending message...
Send us your enquiry today...
Tell us what you need, and we'll respond promptly.
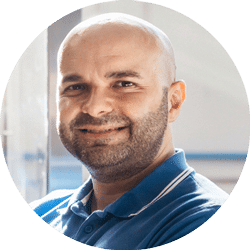
For detailed information
Contact our Sales Director Marco Solferini by calling
+39 0141 162 0091 or +39 0141 74166 (Italy)
+44 1865 520 083 (UK)
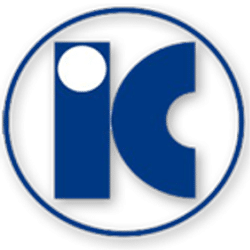
Alternatively request
a quotation
Can’t find what you’re looking for?
Search this site...